In process manufacturing, manufacturers must be able to substitute material due to low material inventory, supply chain issues, product seasonality, or quality sampling. In D365 it is easy to create a scenario where consumable materials can be substituted for a production order.
There are three methods for substituting materials during the production process:
1. Date-Based
By date on the Formula line, when one material is substituted for another after a specific date
- From and to validity dates can be set up on Formula lines using the From and To Date fields.
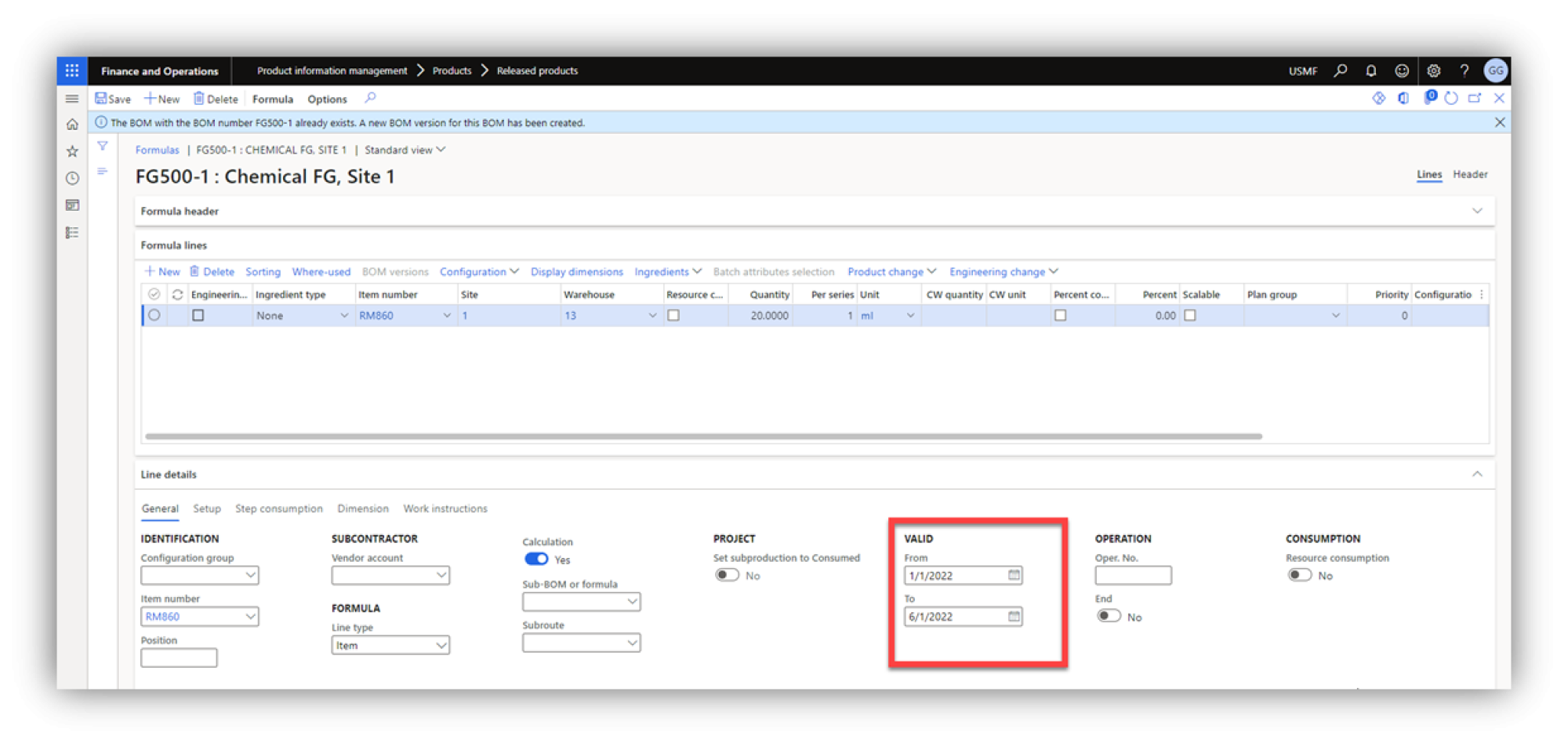
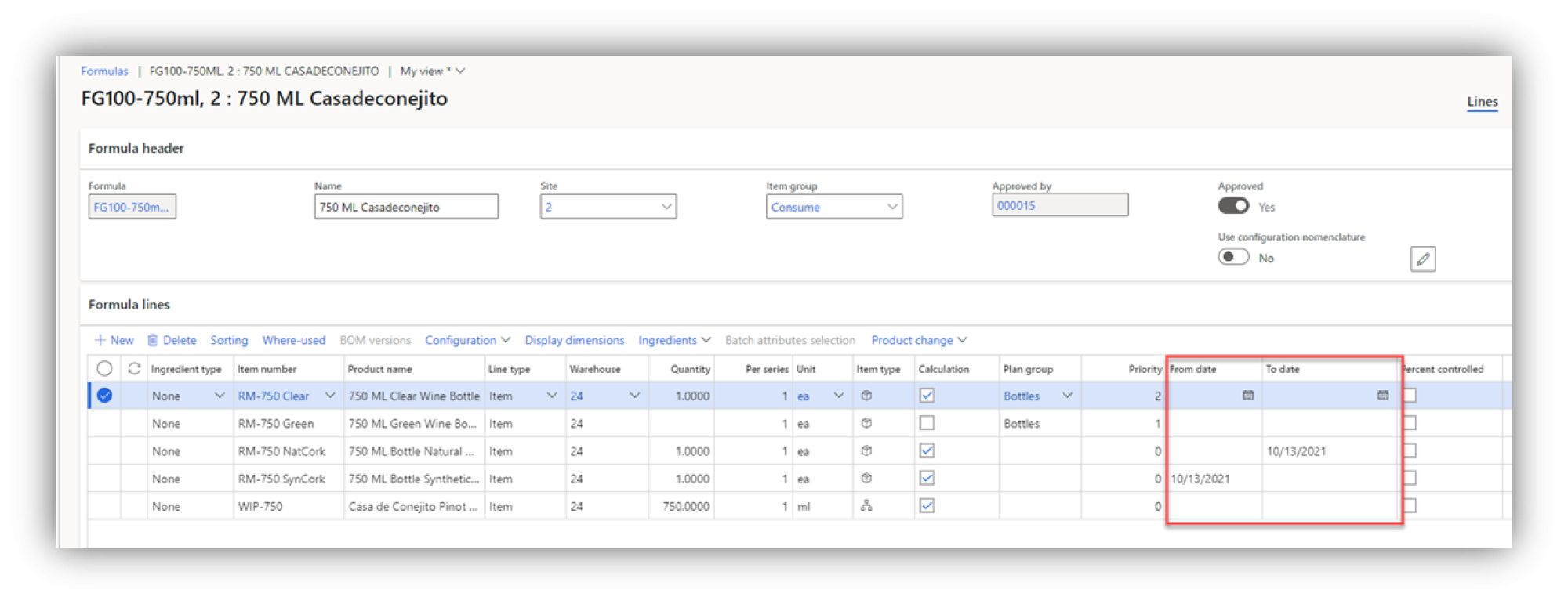
2. During Master Planning - Automatic Substitution
During master planning, a material in a formula may be substituted with a different item, because the preferred item is out of stock. When this occurs, Master Planning will use the Plan group and Priority fields that are on the formula lines to determine which product to substitute. Planning groups are used to connect items that will be substituted during Master Planning. Planning groups are available to use only if you are using formulas, not BOM’s
- In the example below, we occasionally have a situation where we are out of our favorite Green bottles and must use the Clear bottles that we have in stock. We want Master Planning to automatically include the Clear bottles when the Green bottles are not available. This type of substitution takes place in the MRP run using the Formula line Plan Group and Priority settings.
- Material substitution by planning is controlled by the Plan group and Priority fields on the formula lines.
- Plan groups help establish ingredient substitution based on a priority. Items associated with the group are substituted in ranked priority order during master Scheduling based on inventory availability.
- The Item which has the highest priority (lowest number) will be considered first. In the formula lines example below, the Green bottle has the highest priority with a Priority code of 1.
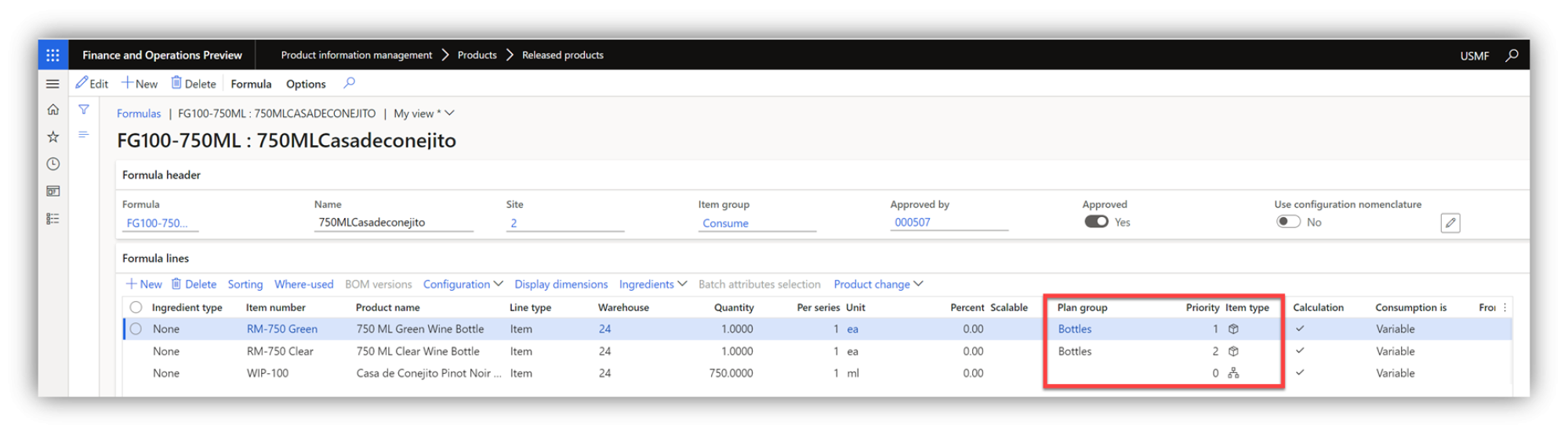
- When the inventory for both bottles is equal to zero, MRP recommends the purchase of the Green Bottles (highest priority item).

- When the inventory for the Clear bottles is > zero but inventory for the Green bottles is zero, MRP uses the Clear (lowest priority) bottles and does not recommend a purchase order.

- When the inventory for both bottles is > zero and either bottle can satisfy the requirements, MRP uses the Green (highest priority) bottles and does not recommend a purchase order.

- The Production order Formula from MRP includes both bottles, but only the Green bottle has an Estimated Quantity.
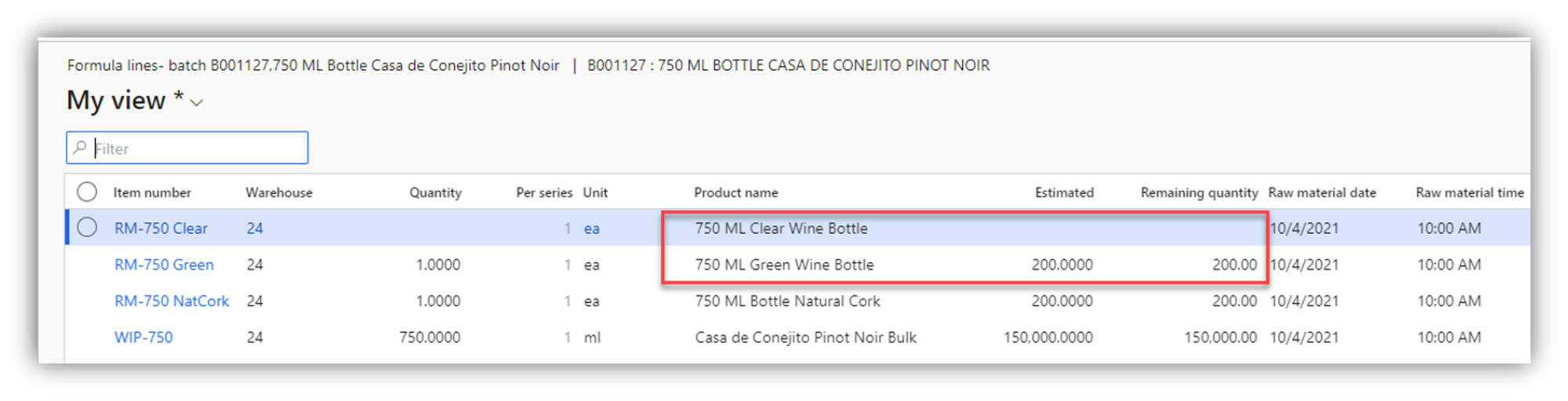
3. During Production - Manual Substitution
During production, when a material is unexpectedly out of stock it can be manually substituted with a different material.
- Material can be added to the Formula for an open production order. If the production order has a status of Started, users are asked to re-estimate the order when they add a new item to the production Formula. After the material is added, a new picking list can be created for the new item.
- You don't have to add the new material to the production Formula. Instead, you can add it directly to the production picking list. Then, when the picking list is posted, the new material will be consumed.
This describes the three methods for Substituting materials in D365.